
Collaboration
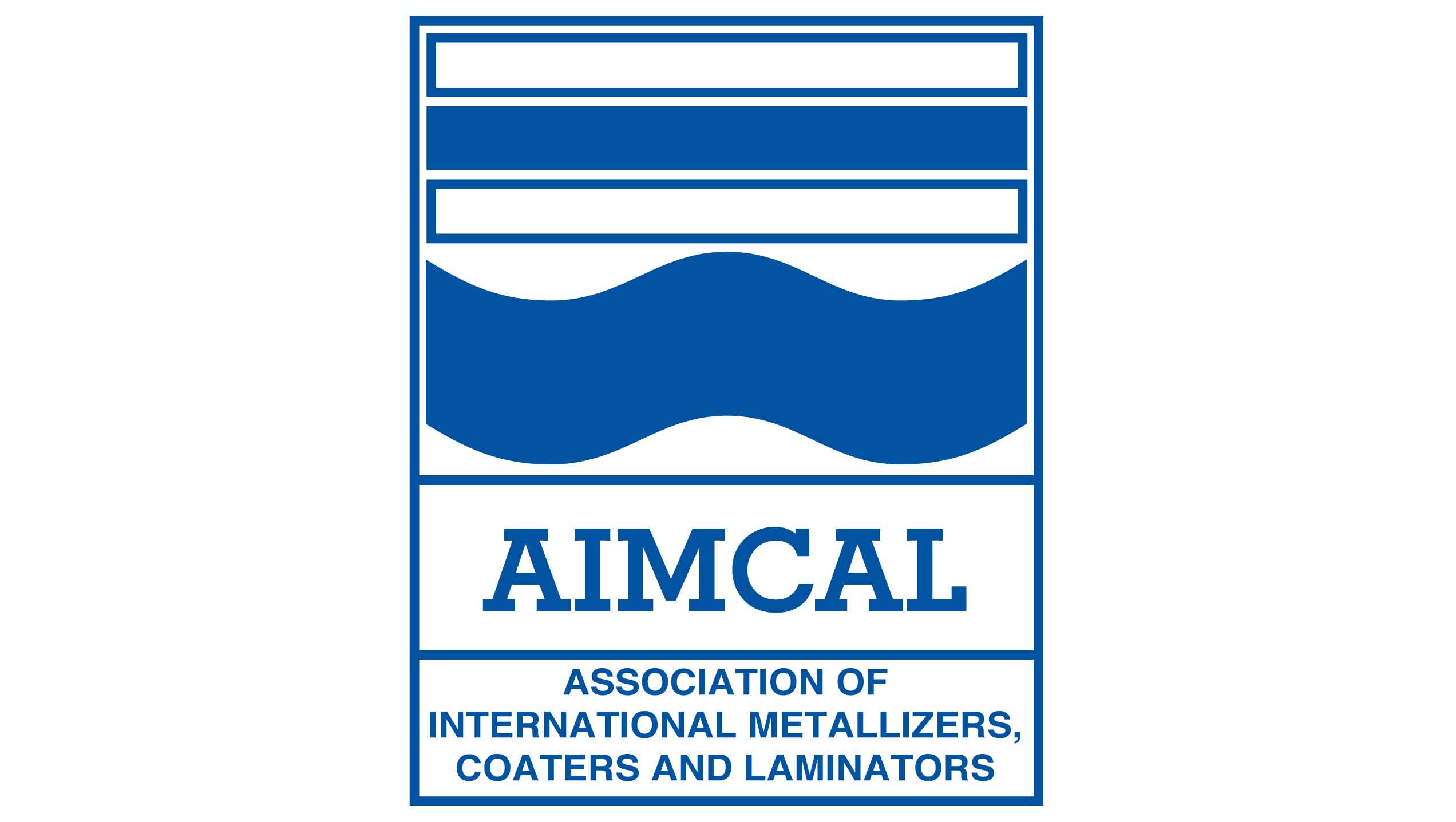
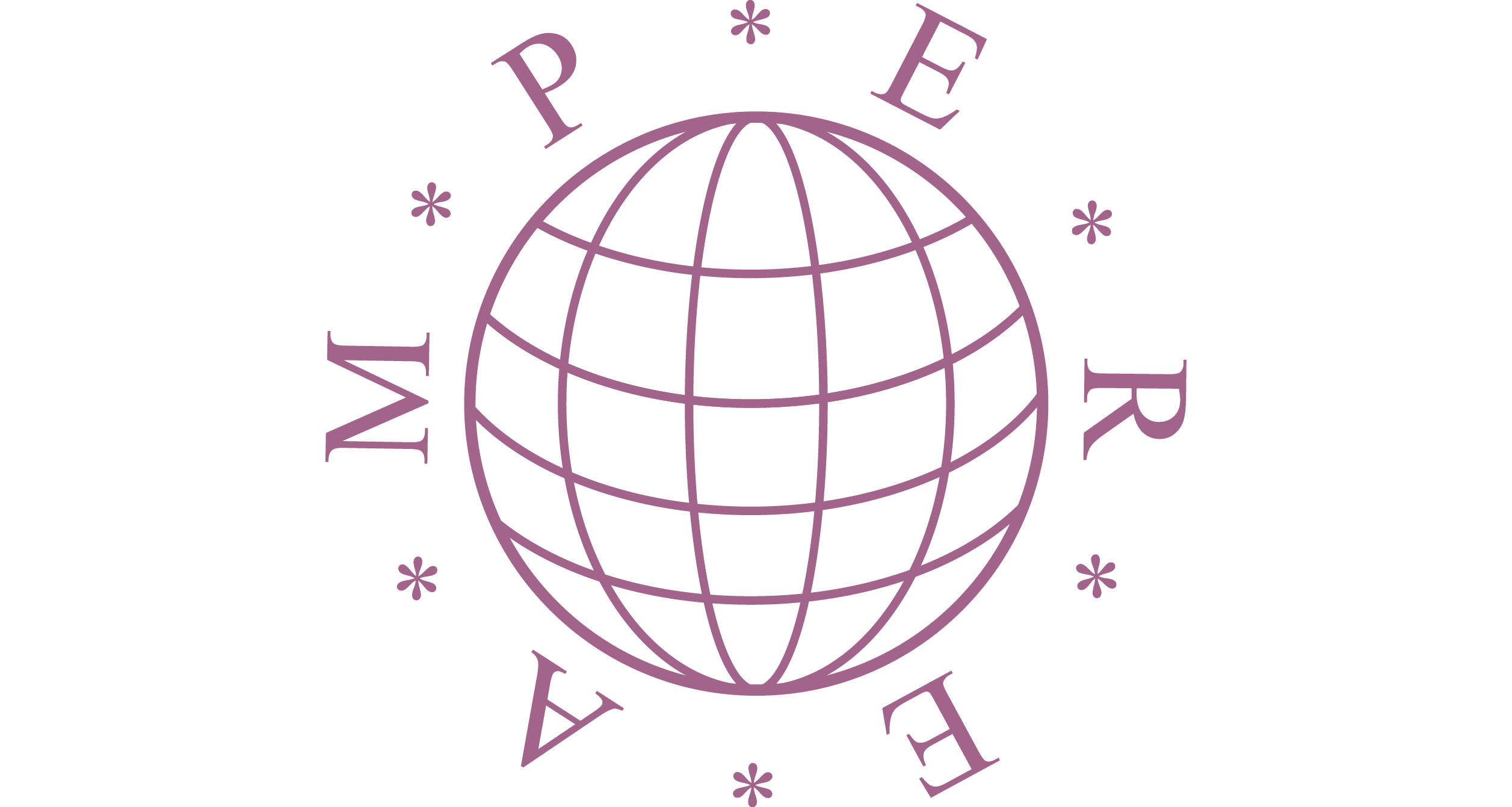
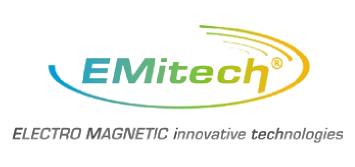
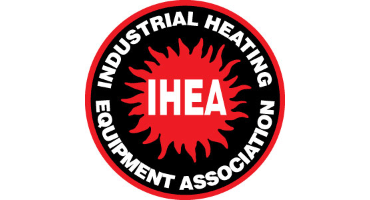
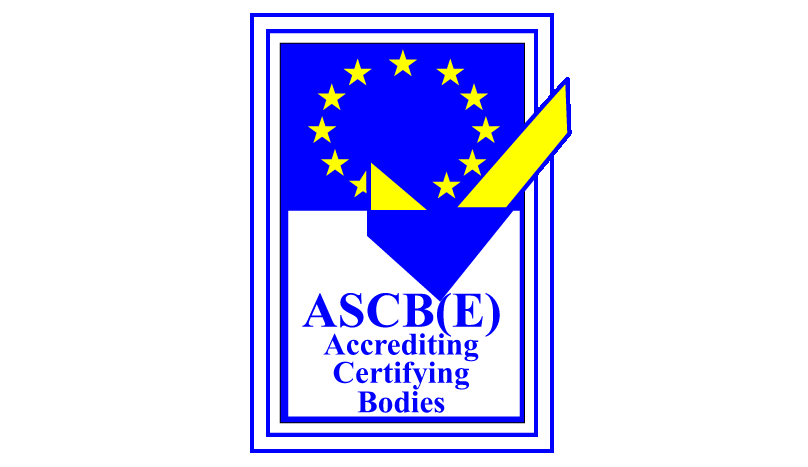
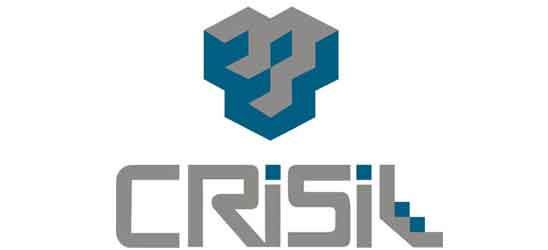
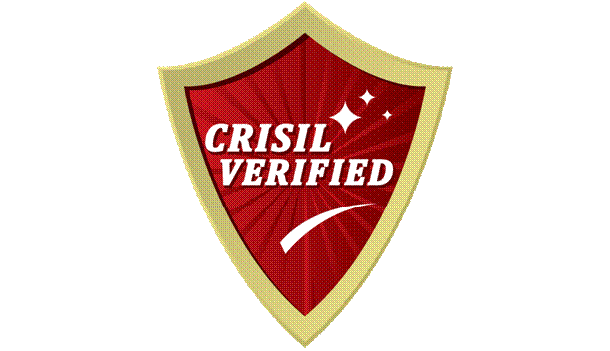
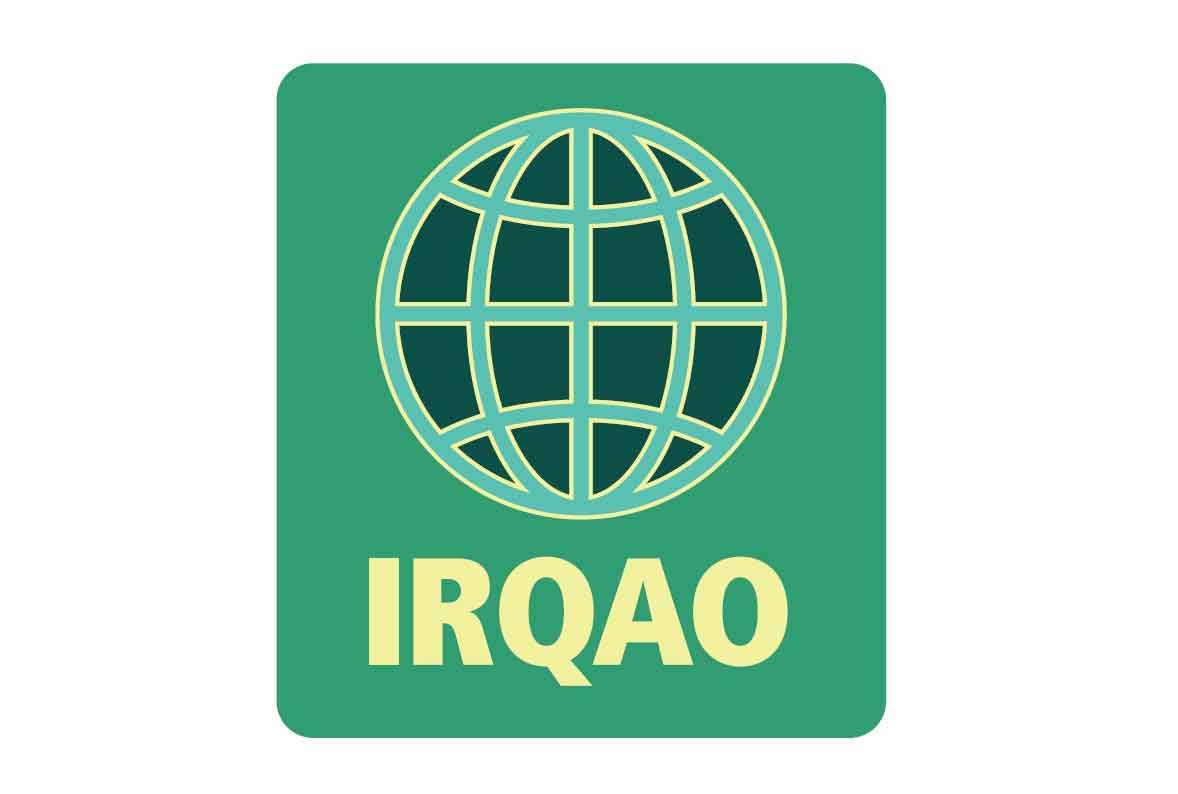

Blog
- Drum Heating Ovens, Controls Viscosity and Prevents Freezing
- Heating and cooling systems, to facilitate all Industrial functions
- Increase Shelf life of your food products- use Dehydrators
- A Catalyst to Longevity of your Product – Industrial Coating
- Relevant Aspects of Industrial Ovens
- Drying of Food
- Microwave in rescue– Preventing Foods, Herbs, Seeds and Spices from contamination
- Industrial Fabric Coating- Making More than Just Piece Cloth
- Making Your Food More Tastier
- Making You Dose of Tablet Consumable- Table Coating
- Understanding Coating and Techniques of coating!!!
- Why and How to temper a Glass
- Microwave Heating System for the Synthesis

Event Calender

Send us a message

Whatsapp Us
Products
- Industrial Dryers
- Coating Lines
- Process Equipments
- Mixing Kettle Plant
- Dehydrators
- Coating & Impregnation Plant
- Heating & Cooling Solutions
- Sterilization and Disinfestations System
- Microwave Heating Systems
- Industrial Heaters
- Fuel Fire Heating System
- Industrial Heating Equipments
- Hot Air Generator
- Radio Frequency Heating System
- Umbrella IR Dryer
- Electric Oven for HT/LT Motors
- Microwave Solid Tyre Pre-Heating
- Plastic Annealing Oven
- PLC & Automation Panel
- Infrared paper coating & Drying
- Infrared Heating Equipment
- Gas Infrared Heating System
- Infrared Heating Systems
- Infrared Heaters
- Lab Equipments